Most wells will suffer from corrosion, scale build-up and/or other environmental complications during their lifetimes. If left untreated, these problems can reduce production efficiency and potentially compromise well barriers. Such environmental complications are typically resolved through chemical injection. Simple injection systems utilize an injection line in the annulus and a check valve in the side of the completion, Fig. 1. These setups are effective in shallow wells with high reservoir pressure, but issues resulting from the “U-tube” effect can arise in most other wells.
The use of modern chemical injection valves (CIVs) with built-in anti-U-tube functionality (or in combination with a separate anti-U-tube device) enables operators to address this problem. In permanent injection systems, which are typically installed during well construction, the CIV is required to perform throughout the life of the field. However, this can be a challenge, as downhole conditions often change substantially over the well’s lifetime. CIVs are also subject to extremely harsh conditions, which can increase the risk of failure. If the valve is not retrievable, there could be a need to pull the entire injection system, increasing costs and impacting production. Monel 400 Hydraulic Control Line
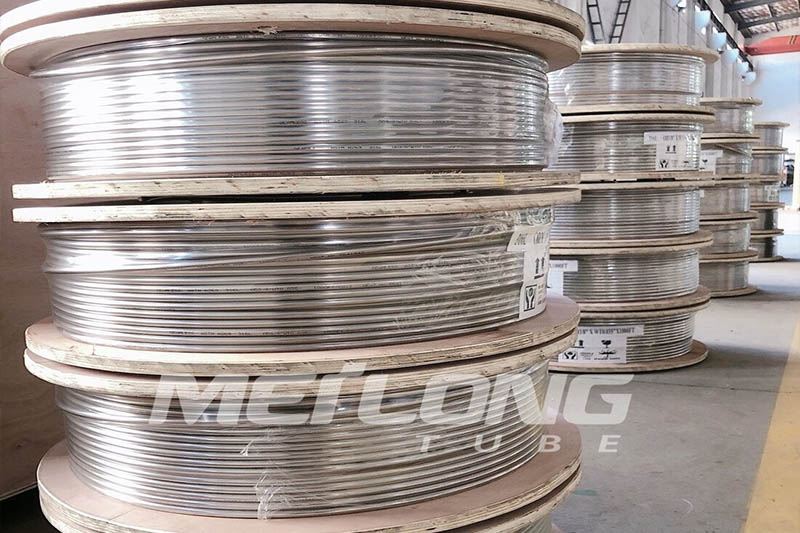
Retrievable CIVs continue to gain traction, as they provide operators with greater operational flexibility than permanent valves. As one of the industry’s leading suppliers of CIVs, TCO has worked extensively over the years to address gaps in the market and meet the evolving needs of its customers.
The latest innovation in the portfolio is the API 19CI-qualified FNR (fall-through protection, Non-return, Retrievable) injection valve. The FNR injection valve has a pressure rating of 10,000 psi. It can operate at temperatures up to 150°C and su pply up to 5,000 psi backpressure. The first application of the FNR valve took place earlier this year, marking the first successful installation of the API 19CI-qualifed retrievable CIV on the Norwegian Continental Shelf (NCS).
Chemical injection challenges. The U-tube effect is prevalent when heavy treatment chemicals are being injected into a formation with low reservoir pressure. In such cases, the weight of the liquid column in the line is sufficient to overcome the reservoir pressure, causing chemicals to hydrostatically fall out (i.e. siphon) into the wellbore.
This creates a vacuum at the top of the line, as space is created in the closed system. The reduction in pressure can cause chemicals to boil, impacting their treatment properties and reducing their efficacy. It also can lead to the formation of solids and potential injection line blockages. More critically, many chemicals become considerably more corrosive when they boil, which can cause failure of the injection line and even the surrounding casing and tubing, resulting in the loss of well barrier integrity and potentially catastrophic failure of the well.
A standard solution to address the U-tube effect is to place a second check valve featuring a powerful spring at the base of the injection line. The back-pressure valve maintains a positive pressure preventing hydrostatic fall-through. However, conventional back-pressure solutions will not hold positive pressure at low flowrates. They also will not hold consistent back pressure in the event of changes in flowrate, nor do they fully close when the injection flow is stopped. All of these issues increase the likelihood of the U-tube effect and its associated problems.
Another issue with conventional chemical injection solutions is that the basic valve design is often not suitable for use in situations with high pressure differentials. As treatment fluid passes through the valve, the significant drop in pressure causes bubbles to form. When the bubbles collapse, they create an implosion force, which erodes the surface of the ball. This process is known as cavitation and will ultimately result in the valve failing to close properly (again causing the U-tube effect). Furthermore, conventional chemical injection devices have difficulty maintaining a consistent injection rate, resulting in ineffective treatment of the well and the unnecessary wasting of chemicals.
FNR valve development. Since 2012, TCO has been among the leading companies when it comes to downhole chemical injection valves. One of the key products in the chemical injection portfolio is the FN back-pressure valve, which has a strong track record on the NCS and abroad.
The FN provides a closing force that increases as inlet pressure is applied, making the module leak-tight, even in low or no flow conditions. It is ideal for deep installation and for overcoming the U-tube effect. Making use of a reliable and field-proven modular approach, the FN valve is supplied with TCO’s ISO 14998 V0 barrier-qualified HN-Series (high integrity, non-return) check valves to complete the well barrier envelope.
This provides operators with a purpose-built overall injection solution that addresses many of the issues faced with conventional injection solutions, including leakage, U-tubing and non-consistent backpressure. With the increasing need across the offshore industry to further improve operational flexibility, t he next logical step was to package the FN valve into a retrievable chassis. The development for the new FNR valve began in 2021, Fig. 2.
Throughout 2022, TCO tested and verified the design of the FNR valve and qualified it in accordance with Equinor’s TR2385 and API 19CI. The API 19CI specification was released in 2019 and states the requirements for chemical injection devices intended for use in the worldwide petroleum and natural gas industry. This includes requirements for specifying, selecting, design verification, validation testing, manufacturing, quality control, testing, and preparation for shipping of chemical injection devices.
The FNR valve was developed with support from SLB, who supplied mandrel and running tools in the API test and field trial. This enabled TCO to increase the side pocket mandrel offering, to meet the enhanced criteria.
The project objectives to design and develop and qualify the FNR valve to API 19CI were met satisfactorily. All tests were completed successfully, and the results were within the acceptance criteria specified by TCO, Equinor and API 19CI standards. The primary advantage of the FNR valve is that it provides operators with the ability to retrieve and change the valve or anti-U-Tube mechanism at any point during the well’s lifetime, which can save operators the potential costs of recompleting a well due to CIV failure. As previously stated, the valve has a pressure rating of 10,000 psi and can operate at temperatures up to 150°C and supply up to 5,000 psi back pressure , making it suitable for a broad range of applications.
To date, TCO has received orders for eight FNR valves. Five of the valves have already been delivered to clients for installation. The first application took place in April of this year for a major operator on the NCS, Fig. 3. The customer required a retrievable CIV, due to changes in well parameters. After installation, the integrity of the control line was tested and verified against the FNR’s U-tube module. The project marked the first successful installation of the API 19CI-qualifed retrievable CIV on the NCS and satisfied all customer requirements.
Ensuring optimal CIV selection. Deciding the optimal CIV setup and how much (if any) back pressure is needed for the chemical injection lines requires evaluation on a well-by-well basis. In some cases, CIV selection can differ for individual injection lines in the same well. Chemical weights vary and are sensitive to downhole changes. As wells deplete over time, variations occur in temperatures, wellbore pressures, and shut-in wellbore pressures.
Topside pump pressure capacity also can be a challenge for some clients, making it even more critical to pinpoint as low a back pressure value as possible without U-tubing at any well stage. In addition, high flowrates in smaller control lines will increase fluid speed. At high speeds, friction can start to become a factor, adding additional strain (pressure) for the topside pump to deliver the requested chemical injection flowrate. TCO has extensive experience supporting and advising clients on how best to address these problems by selecting the optimal CIV setup.
A step-change advancement . Chemical injection plays a critical role in enhancing the performance and longevity of wells. As the oil and gas industry continuously seeks ways to optimize production and address various challenges, the demand for chemical injection solutions that can reduce costs and provide greater operational flexibility continues to grow. While CIVs are often not prioritized to the same extent as higher-cost completion systems, the impact they can have on production and OPEX is still significant. This is particularly the case in the event of CIV failure in a permanent injection system.
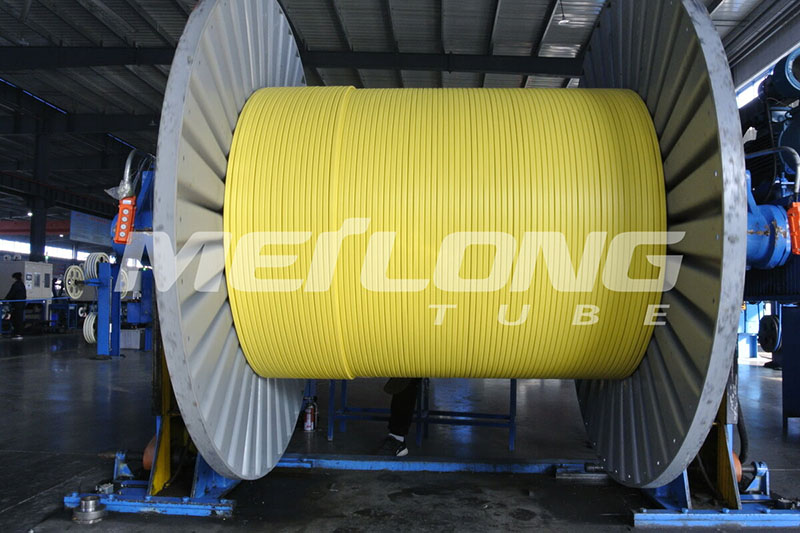
N08825 Hydraulic Control Line Tubing The development and successful installation of the FNR valve represents a step-change improvement in well completions. Its qualification to API 19CI sets a new standard for injection valves and will undoubtedly drive further advancements in the industry, benefiting operators and the industry as a whole.